Hello again, Explorers!
This is Anton from This Way — back again for yet another interview with an important person from our ICE project.
“Waitaminute,” I hear you say. “Didn’t you already interview the whole This Way team??” Yes, but we have an important honorary member that we haven’t talked to yet:
The incredibly talented insert designer for ICE: Matt Healey.
ANTON: So who is Matt Healey??? Can you tell us a little about yourself to our audience?
MATT: So, I am an ex-engineer. I did my undergrad at RPI in physics. I spent a bunch of years designing weapons of mass destruction, went back to business school at Carnegie Mellon, bounced around the high tech industry for a while, and eventually I retired. And in retirement… I basically have always been an avid gamer. And I saw a lot of games that I kind of thought didn’t have great inserts and I could do a lot better. So I started designing them kind of as a hobby on my own. And then one thing led to another, and now I’ve ended up designing a lot of inserts for a lot of other games. ICE was one of them. And that’s how I ended up getting working with This Way!
ANTON: So how did the involvement with This Way start? I’m curious how you began designing the insert for their first game…
MATT: It’s actually a really boring story. I was designing inserts for a bunch of different game creators, and I was looking through the Kickstarter list of new launches at one point, and ICE looked interesting to me. The concept of picking the sheets of ice up and mining into it and the 3-dimensional board… it looked like it’d be a fun game to play, and it looked like it would be an interesting challenge from an insert perspective. So I simply sent them a message through Kickstarter and said, “If you’re looking for a custom insert, I’ve done a bunch by now, and your game looks interesting. Maybe you’d be interested in having me work with you on it.” And that was really that. They reached back, and the rest is history, as they say.
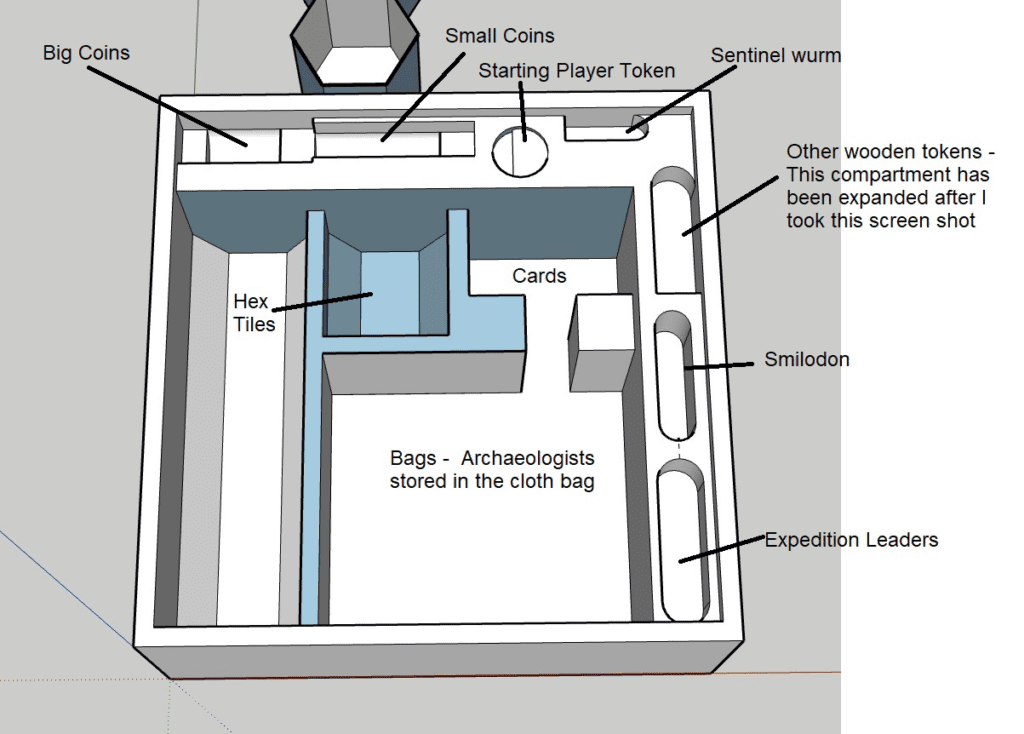
ANTON: Have you designed inserts for other boardgames? If so, which ones?
MATT: At this point, I’ve probably done somewhere between 40 and 60 inserts.
ANTON: Wow!!
MATT: I maintain a website where you can see a lot of them listed: mess-axp.com
Mess is, for reference, my trail name name. I have hiked the Appalachian Trail, and that was my trail name. And AXP is Alpha Chi Ro. That was my fraternity in college. In terms of other games, I’ve done, I’ve done a lot. I do a lot of inserts for Conor [McGoey] from Inside Up Games. They make excellent games and I love working with Conor — he’s a great guy. I’ve done Machina Arcana, their third edition, which was a very challenging insert — very fun to do. But I think the crowning achievement in terms of the size of the game and the popularity of the game was Frosthaven. I did the stock insert that comes with Frosthaven, and that’s a game almost everyone has heard of. That one was very challenging, mainly because the game is physically very big. But I will say working with Price [Johnson] and Cephalofair games…. so much fun. They are really great people. I can’t say enough good things about Price.
Stock insert for Frosthaven
ANTON: How does one go about designing an insert?? What kind of knowledge and tools are needed?
MATT: So the sarcastic answer for the special skills and how you go about designing an insert really comes down to…. First, you really need a mild case of OCD. You really need to obsess about organization. You think that there’s a place for for everything. And if your games aren’t organized, then it’s kind of a mess. So you kind of need to want things to be organized. I also have kind of a hatred of games that take too long to set up, and inserts that are bad and don’t assist in the setup process. This is kind of how I got into designing inserts, because there was a game called Adrenaline, which I really like because it’s fun, it’s silly, you run around, you shoot your friends, and it’s not personal. But the insert was not very good. It was nonexistent. And so I, on my own, designed a wood insert for that. I had dataless laser cut it and in exchange for the IP for the insert. And then from there I started designing for them. And then eventually I designed my first vac-form insert for Shiver Me Timbers. I’ll always have a great spot of pride… that game will always sit in a place of honor on my shelf. Because Michael [Vitkovsky] was the first of the game creators who trusted me to design their insert, even though I’d never done vac-form before. So I spent some time and learned how to do vac-form. In terms of other tools, I use SketchUp. And you really do have to understand how to use 3D CAD. That’s not something that is easy, but if you think a certain way — maybe the OCD helps — you can do it. And so you need to understand a CAD program or else you’re not going to get anywhere…

ANTON: Are there any special challenges in designing an insert? (Especially one with such a unique board, like ICE…)
MATT: The biggest of all the special challenges that you have to deal with, really, is understanding the tradeoffs. There’s a lot that you can do with an insert, but for everything you do, there’s a tradeoff. And so you kind of have to understand the game creator, what their vision is, the rule book… I like to read the setup before I start designing an insert, because that’ll dictate a lot of things. Am I making things mainly player tray focused? Are there communal components? Are trays going to get taken out of the box? All of those kinds of things will help guide an insert design, but you have to realize that everything you do has a tradeoff. And then there’s a lot of things that you just can’t do because vac-form plastic won’t allow it. So you can come up with the best insert and the best design, but if it can’t be manufactured, it’s no good. So understanding what can be manufactured and what can’t be manufactured is probably the thing that took the longest for me to really understand and how that manufacturing process goes. So that’s possibly the biggest thing you got to worry about. And there are way too many rules and guidelines to get into here in terms of, well, you could do this, but then it won’t be able to be manufactured. Or in order to manufacture it, you have to do the following. I do want to say to everyone out there who says, “Well… the insert could clearly be done better this way.” Maybe, maybe not. Keep in mind, there’s a lot of things that are dictated by manufacturing.
Panda’s first manufacturing sample of the ICE insert.
ANTON: This Way is planning to go more eco-friendly with future games and components, which means a traditional plastic insert like the one for ICE might not be in the cards. Any suggestions on what we could do with our next games?
MATT: Sustainability is becoming a really big thing. I’m getting a lot more requests for it. And I understand the need to go away, or the desire to go away, from vac-form plastic. I would say there’s two real possibilities in terms of the best way to do sustainability when it comes to inserts. The first is punchboard. You can basically make a punchboard insert that will just use one and a half millimeter thick gray board. You can print things on it and the users can assemble it. It is doable, they are not nearly as sturdy and they can be more expensive than a vac-form plastic insert.
The second is potentially to not provide an insert at all, but rather to design a series of STL files that you can give away to backers of your Kickstarter. They can then 3D print their insert if they want it, or they can modify it and have it look the way that they want. You have to understand that even if I design what I think is a perfect insert, there’s going to be a large percentage of people who don’t like it and they’re going to take the insert out and throw it away. But if I give them an STL file and they don’t like it, they can modify it to the way that they like and then print it themselves — or they can just put things in baggies. So I would say either punch board or print yourself STL files are probably the most sustainable of all the inserts.
ANTON: Thanks so much for answering these questions, Matt, and for giving us an inside look into insert-making!